Architecture
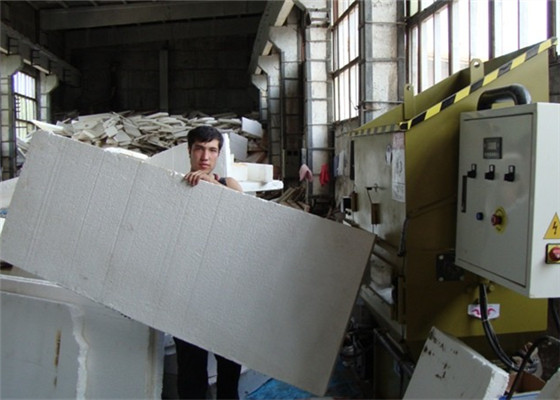
In the construction industry, during the demolition of old buildings, a lot of used building panels will be produced. The waste foam has a significant impact on the 5S management and safety of on-site operations, because foam is flammable and can easily cause fires.
The compression and volume reduction equipment provided by GREENMAX can reduce and compress the dismantled waste foam, saving waste storage space and improving on-site 5S management. Meanwhile, the compressed foam blocks can be resold, generating economic benefits.
BASF Chemical Company in Germany has jointly launched a project with other companies to use plastic waste to produce "Styropor Ccycled" to achieve energy conservation and emission reduction.
BASF obtains the material from technology partners, which is converted from plastic waste that would otherwise be used for energy recovery or landfill. This chemical technology for EPS reuse can reduce carbon emissions by 50%. This technology can not only prove that EPS packaging is a material that can be recycled and reused, but also can add EPS waste to the EPS recycling system for reuse.
GREENMAX provides EPS compactors to industries that generate waste EPS, then repurchases these EPS blocks to make plastic pellets, turning these originally expanded EPS into hard plastic to make new plastic products. This is a very popular business model at present, but a one-stop business model like GREENMAX that manufactures EPS compactors, purchases EPS blocks, and manufactures recycled products is rare. At the same time, GREENMAX will design customized waste plastic recycling solutions for customers based on their needs. The design solution includes the crushing, melting, granulation and other processes of waste foam, as well as the selection and layout of equipment. This is one of the reasons why GREENMAX has become a popular machinery brand.