Beverage
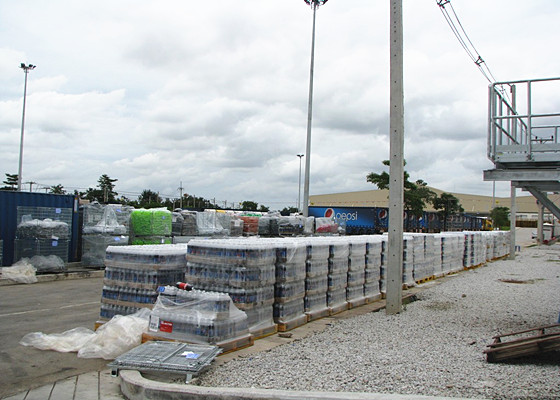
In beverage filling factories, a large number of unqualified beverage bottles (poor bottle quality, incorrect label printing, etc.) will be produced. These defective products are mainly filled with liquid bottles and empty bottles. For filling factories, these two types of waste are difficult to process. The solution provided by GREENMAX is that liquid-containing bottles can be processed through a bottle dewatering and squeezing machine. While reducing the volume, the remaining liquid in the bottle can be squeezed out. Afterwards, the discarded empty bottles can be compressed and reduced in volume using a baler.
Pepsi-Cola Beverages International Group is a world-renowned American multinational company, ranking first in the beverage industry. The PepsiCo production base in Thailand is the largest production base in the Asia-Pacific region.
Each production line at the Thailand base will produce 1% to 2% defective products during the production process. The team hired a large number of workers to unscrew the substandard bottles by hand and flatten them with their feet. This method results in a lot of labor costs, low efficiency, and extremely high transportation costs. As a result, they were always looking for more efficient ways to handle discarded beverage bottles.
The GREENMAX team designed the GREENMAX P-C350 dewatering compactor according to the requirements of the Pepsi-Cola Group to help the Thailand base solve the PET recycling problem. Subsequently, our team went to Thailand to debug the PET recycling machine to ensure that the machine could operate normally and meet the designed technical indicators and recycling rate. The debugging content included stand-alone machine debugging, personnel training, etc. The GREENMAX P-C350 dewatering compactor can increase production efficiency eight times compared to on-site manual processing, helping Thailand's Pepsi save 80% of transportation costs and a large amount of waste disposal costs.